Peter Benner
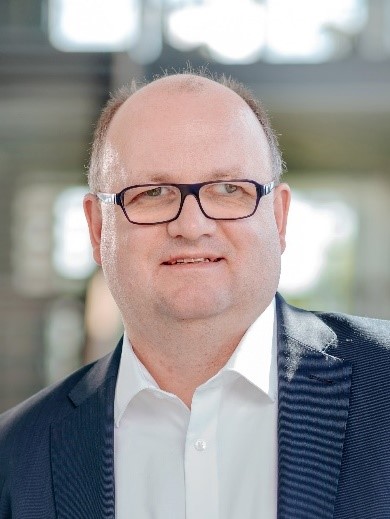
Prof. Dr. Peter Benner
Session: Systems Engineering and Computational Methods
Title: Reduced-order Modeling Enables
Digital Twins for Smart Process
Engineering
Peter Benner received the Diploma in mathematics from the RWTH Aachen University, Aachen, Germany, in 1993. From 1993 to 1997, he worked toward the Ph.D. at the University of Kansas, Lawrence, KS, USA, and the TU Chemnitz-Zwickau, Germany, where he received the Ph.D. in Mathematics in February 1997. In 2001, he obtained the Habilitation (Venia Legendi) in Mathematics from the University of Bremen, Germany. He was an Assistant Professor with the University of Bremen, Germany, from 1997 to 2001. After spending a term as Visiting Associate Professor with the TU Hamburg-Hamburg, Germany, he was a Lecturer in Mathematics with the TU Berlin, Germany, from 2001 to 2003. Since 2003, he has been a Professor for Mathematics in Industry and Technology with the TU Chemnitz. In 2010, he was appointed as one of the four Directors of the Max Planck Institute for Dynamics of Complex Technical Systems, Magdeburg, Germany. Since 2011, he has also been an Honorary Professor with the Otto-von-Guericke University of Magdeburg, Germany. He is a SIAM Fellow (Class of 2017).
Peter Benner’s main research interests include Scientific Machine Learning with a focus of learning dynamical systems from data, Numerical and Multi-linear Algebra including in particular large-scale and low-rank tensor computations, Model Order Reduction of dynamical systems using intrusive and non-intrusive methods, Reduced-order and Data-driven Modeling of time-dependent processes, Numerical Methods in Systems and Control Theory, PDE Constrained Optimization, High-performance and Power-aware Computing.
Reduced-order Modeling Enables Digital Twins for Smart Process Engineering
Smart process systems heavily rely on virtual process models for optimizing the process yield and the product purities, designing feedback controllers to guarantee stable operations and attenuate disturbances, and for process surveillance during plant operation. Hence, digital or virtual twins of all the processing steps are needed. As many of the process steps include exothermic reactions, complicated reaction kinetics, fluid-structure interactions, particle aggregation, nucleation, breakage and growth described by complex population balance models, etc., the mathematical models often consist of coupled systems of time-dependent nonlinear partial differential equations (PDEs). Hence, surrogate models are needed that allow optimization and control design with limited time budgets, and real-time computations for fault diagnosis and surveillance. Model order reduction of dynamical process models is an enabler to design computationally efficient surrogates for real-time operation. Many recent advances in model order reduction of nonlinear dynamical systems allow the application to the coupled PDE models occurring in process engineering. We will briefly sketch the underlying mathematical methodologies and demonstrate the power of these techniques using several problems from chemical engineering.